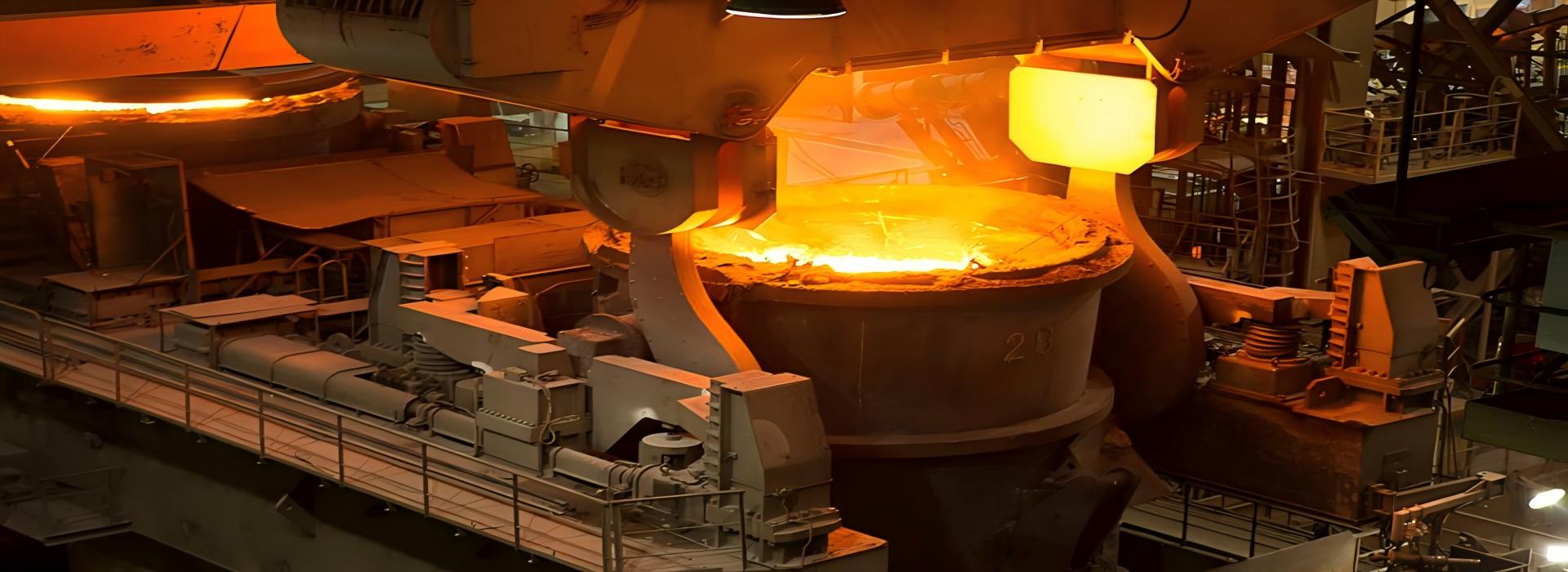
Torch Cutting Nozzle
The torch cutting nozzle for continuous casting is the core component of flame cutting. It is responsible for mixing gas and oxygen and forming a high temperature flame, which directly determines the cutting efficiency, incision quality and energy consumption. Its design and material need to adapt to the harsh environment of high temperature, oxidation and slag impact.
cutting nozzle structure and key parameters
parameter | Typical scope / design key points | act on |
The aperture design | -Preheat hole: φ0.8~1.5mm (gas mixed with oxygen)
-Cut oxygen hole: φ1.5~~3.0mm (center hole, high-pressure oxygen injection) |
Control of the flame shape and the cutting oxygen flow rate |
Number of holes | -Single hole: standard cut
-Porous (3~6-hole ring distribution): improve preheating uniformity (suitable for thick slab) |
Reduce the preheating time and reduce the slag hanging rate |
Length / cone | -Total length of 50-120 mm
-Exit taper 30°~60° (optimized oxygen beam focusing) |
Increase the cutting oxygen kinetic energy and reduce the incision width |
cooling-down method | -Water cooling sleeve (circulating water cooling of copper pipe)
-Air-cooled (compressed air injection) |
Prevent high-temperature ablation and prolong the service life |
Install the interface | -Thread connection (M12~M24)
-Quick card buckle (replacement time <30 seconds) |
Ensure sealing and easy maintenance |
Material materials and coating techniques
Material type | characteristic | applicable scene |
Pure copper (T2 / T3) | Good thermal conductivity (398W / m · K), easy to process, low cost | Low-load cutting (<200mm thickness) |
Chromium-zirconium copper (CuCrZr) | High temperature strength (600℃ tensile 150MPa), resistant to oxidation | High-frequency cutting (> 20 times / shift) |
Ceramic composite copper | Al ₂ O ₃ / ZrO ₂ coating on copper matrix + surface (temperature resistance> 1300℃), and the life is increased by 2~3 times | High-alloy steel, stainless steel cutting |
Tungsten copper alloy | Tungsten skeleton + copper penetration (thermal conductivity / wear resistance), strong slag erosion | High-melting point steel type (such as high-speed steel) |
performance index
metric | critical field | Selection reference |
Temperature resistance limit | Copper alloy: 800~1000℃
Ceramic coating: 1200~1400℃ |
Select the material according to the casting temperature |
Lifetime (number) | Pure copper: 500 ~ 1,000 times
Chromium zirconium copper: 1500 ~ ~3000 times Ceramic composite: 3000~5000 times |
High yield line preferred long life material |
cutting speed | 100mm thick slab: 200~300mm / min
300mm thick slab: 80 ~ 150 mm / min |
The larger the aperture, the higher the cutting speed |
Gas adaptation | -Propane / natural gas: standard copper alloy nozzle
-Coke oven gas: need for sulfur resistant coating (e. g. Ni-P coating) |
Prevent the corrosion of fuel gas impurities |
Selection advice
scene | Recommended slit type |
Large-section slab (> 300mm) | Porous chromium zirconium copper cutting nozzle + water cooling sleeve, cutting oxygen aperture diameter of 2.5mm |
High-alloy steel / stainless steel | Ceramic composite nozzle, annular distribution of preheating holes (6 holes) |
Cut the production line at a high frequency | Quick change card buckle type tungsten and copper cutting nozzle, combined with an automatic cleaning device |
Low-cost maintenance requirements | Standard pure copper cutting nozzle, regular coating repair (every 300 times) |
Our company has many years of experience in the production and marketing of torch cutting nozzles, and we have professional technical personnel who can produce and process according to customers’ individual needs. The above parameter data can be used for reference, if you have specific needs, please feel free to contact us.