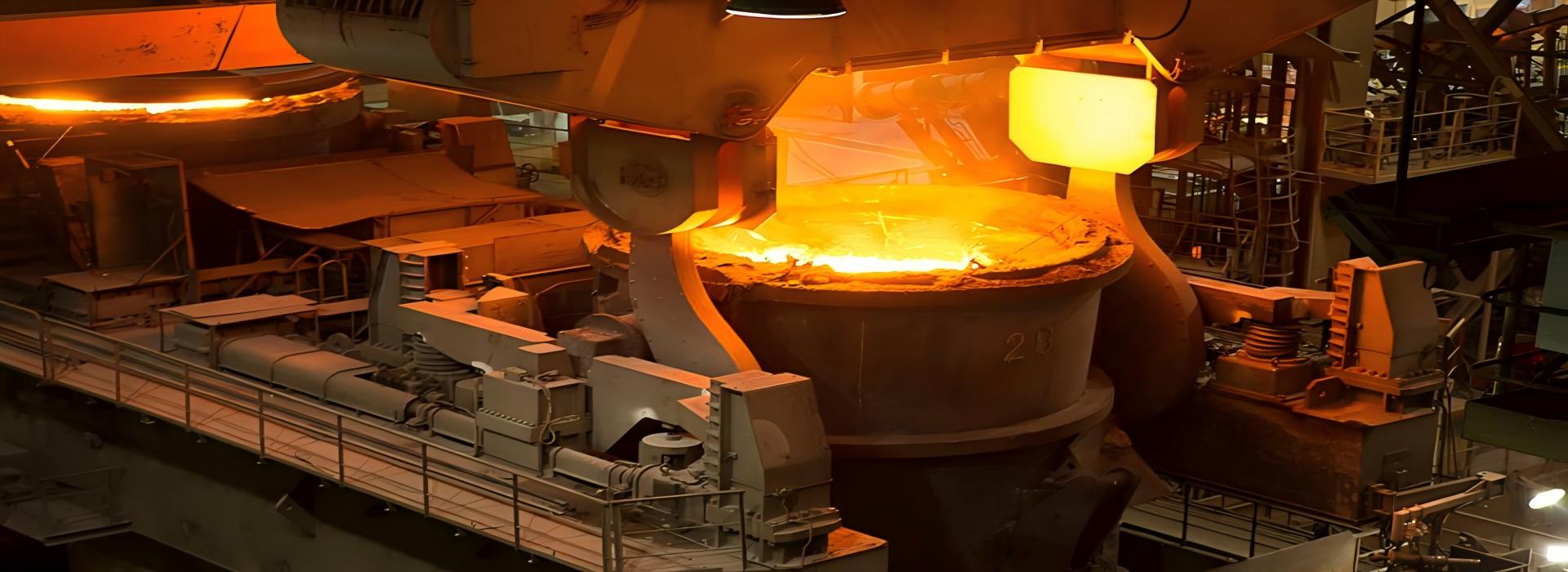
Electric Arc Furnace
Electric Arc Furnace (EAF) is a kind of metallurgical equipment which utilizes electric energy to generate high temperature arc through graphite electrodes to melt steel scrap or directly reduce iron. It is the core equipment of modern short-process steelmaking, especially suitable for steel production with scrap as the main raw material, featuring energy saving, environmental protection and high flexibility.
- Working principle
Arc heating: high-temperature arc (temperature up to 3000℃ or more) is generated between graphite electrode and charge (scrap, etc.), and the metal is melted directly through the arc heat.
Resistance heating: After the formation of the molten pool, the electric current passing through the liquid metal generates resistance heat, which further heats up the molten steel.
Chemical energy assistance: blowing oxygen combustion or adding carbon powder and other chemical reactions to release heat, assisted warming.
- Main structure
Furnace body: It is composed of steel shell lined with refractory material and divided into furnace bottom, furnace wall and furnace cover.
Electrode system: 3 lifting graphite electrodes (three-phase alternating current), the arc length is controlled by adjusting the electrode position.
Tilting device: tilt forward when steel is discharged, tilt backward when slag is discharged.
Dedusting system: Handle the smoke and dust generated in the smelting process (e.g. bag dedusting or electrostatic dedusting).
Auxiliary equipment: Oxygen gun, carbon powder blowing device, alloy charging system, etc.
- Smelting process
Charging: Scrap or DRI is loaded through the furnace roof or door.
Melting phase: the electrodes are energized to produce an electric arc, and the scrap is gradually melted (energy consumption accounts for 60%-70% of the whole process).
Oxidizing period: Oxygen blowing removes impurities (e.g. C, Si, P, etc.), and foam slag is formed to cover the arc to improve thermal efficiency.
Reduction period (optional): add alloy to adjust the composition, desulfurization, deoxidation.
Out of steel: steel is poured into ladle to enter the refining process.
- Technical characteristics
Flexible raw materials: mainly scrap, can be matched with molten iron, DRI, hot briquetted iron (HBI), etc.
Energy saving and environmental protection: energy consumption of about 350-400 kWh per ton of steel, COâ‚‚ emission reduced by more than 60% compared with the traditional blast furnace – converter process.
Rapid production: the smelting cycle of one furnace is about 30-60 minutes, which is suitable for small-lot and multi-variety production.
High degree of automation: Modern EAF adopts intelligent control system to optimize power supply, oxygen supply and charging.
- Environmental protection measures
Pre-treatment of scrap steel: removing impurities such as oil and non-ferrous metals.
Flue gas recovery: Utilizing waste heat boiler to generate electricity and capture dioxin and other pollutants.
Slag treatment: steel slag is recycled for building materials or road base materials.
   6.  parameters
Parameter name | Typical range/number | Explain |
Furnace capacity | 30 to 400 tons (commonly 50 to 150 tons) | Single furnace steel output. |
Casing diameter | 4~12 meters | Correlated with capacity, such as 100 tons furnace diameter is about 6~7 meters. |
Electrode diameter | 400~700mm (AC three-phase) | The electrode of the ultra-high power furnace is thicker, and the DC furnace has only one large diameter electrode (such as φ700mm). |
Rated power of transformer | 60~150 MVA (ultra high power furnace) | Modern UHP-EAF transformers can have a capacity of more than 120MVA (e.g. 100MVA for a 150-ton furnace). |
Power consumption | 350~450 kWh/t steel | The typical value of scrap steel smelting can be reduced to 300kWh/t if 30% iron water is added. |
Fusing time | 25 to 50 minutes | Depends on feedstock (scrap steel/DRI) and input power. |
Smelting cycle | 40 to 70 minutes | Including loading, melting, oxidation and steelmaking. |
Example: Typical parameters of a 100-ton AC arc furnace
Transformer power: 90 MVA Secondary voltage: 400~900V (20 steps adjustment) Electrode diameter: 550mm Smelting cycle: 45 minutes Annual output: about 700,000 tons (operating rate 85%) |
Our company has many years of experience in the production and sales of electric arc furnace, occupying a leading position in the Chinese market, and sold to Russia, Southeast Asia, Africa and other countries.
The above parameters can be used for reference, if any demand feel free to contact us.