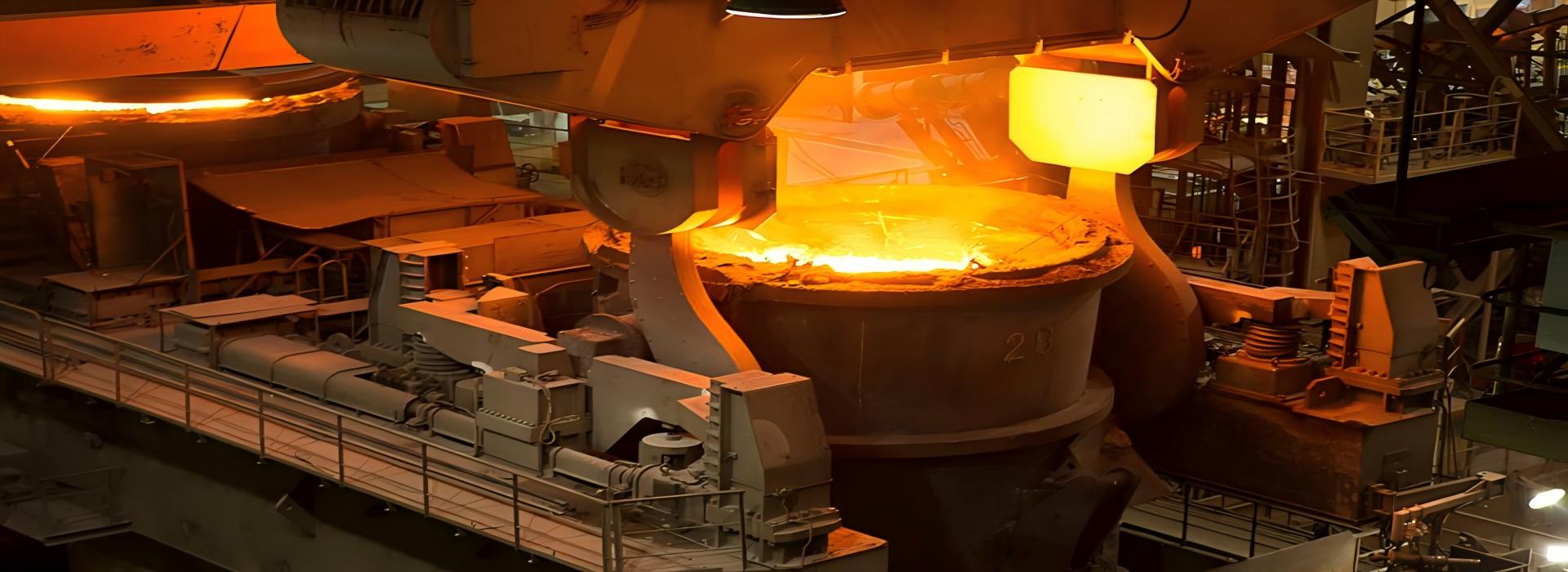
Torch Cutting Machine
Torch cutting machine for continuous casting machine is the key equipment used in continuous casting production line for cutting high temperature continuous casting billet into fixed ruler length, especially suitable for large section casting billet (e. g. slab, large size billet) or high alloy steel without hydraulic shear. It melts the metal by high temperature flame and blows out the slag, and has the advantages of high adaptability and low cost.
1. Equipment structure and core components
assembly | Functional and technical requirements |
Motor&Track | -Drive mode: motor + gear rack or servo drive
-Walking speed: 0.5~5m / min (matching casting pull speed) -Track material: heat-resistant steel (surface temperature: 300℃) |
Gas system | -Gas type: propane (C ₃ H ₈), natural gas (CH ₄), or coke oven gas
-Oxygen purity: 99.5% -Pressure range: gas 0.05~0.15MPa, oxygen 0.4~1.2MPa |
The torch mechanism | -Cutting material: copper alloy (high temperature oxidation resistance)
-Number of torch: single torch (standard) or multiple torch (wide slab synchronous cutting) -Swing mechanism: automatic lift (travel of 100~300mm) |
navar | -Rule accuracy: ± 5mm (encoder positioning)
-Automation function: automatic ignition, fault alarm and remote monitoring -Linkage signal: synchronous with the pulling machine and the conveying roller |
coolant passage | -Water cooling cutting torch: circulating water flow is 2~5m³ / h, water temperature is 50℃
-Track cooling: spray water cooling (prevent thermal deformation) |
Â
2. Key performance parameters
parameter | Typical range | Impact indicators |
Cut the thickness | 100-500 mm (slab), 150~300mm (billet) | Gas / oxygen consumption, cutting speed |
cutting speed | 100-600 mm / min (inversely proportional to the billet thickness) | Production line rhythm, incision quality |
Gas consumption | Propane: 1.5~4m³ / h, oxygen: 10~30m³ / h (single cut torch) | running cost |
The incision quality | -Planarity error: ± 2mm / m
-Hanging slag thickness: 1mm (need secondary cleaning) |
Requirements for the subsequent rolling process |
cut lengths | 6~12m (standard), special requirements up to 18m | Production line compatibility |
3. Fire cutting machine and hydraulic shear contrast
Contrast item | flame cutting machine | Hydraulic shear |
Applicable section | Large section (slab> 300mm), high alloy steel, special-type billet | Small and medium cross section (billet 400mm), general carbon steel |
The incision quality | There is an oxide layer, and the need for secondary treatment | Flat and no oxidation, it can be directly rolled |
Energy consumption cost | High (gas + oxygen consumption) | Low (electricity only) |
Maintain complexity | Medium (replace cutting nozzle and clear slag) | High (hydraulic system seal, blade repair) |
rhythm of production | Slower (cutting speed is thickness-dependent) | Fast (shear period 3~10 seconds) |
Our company has many years of experience in the production and marketing of torch cutting machine, with professional technical personnel, according to the individual needs of customers, production and processing. The above parameter data can be used for reference, if you have specific needs, please feel free to contact us.