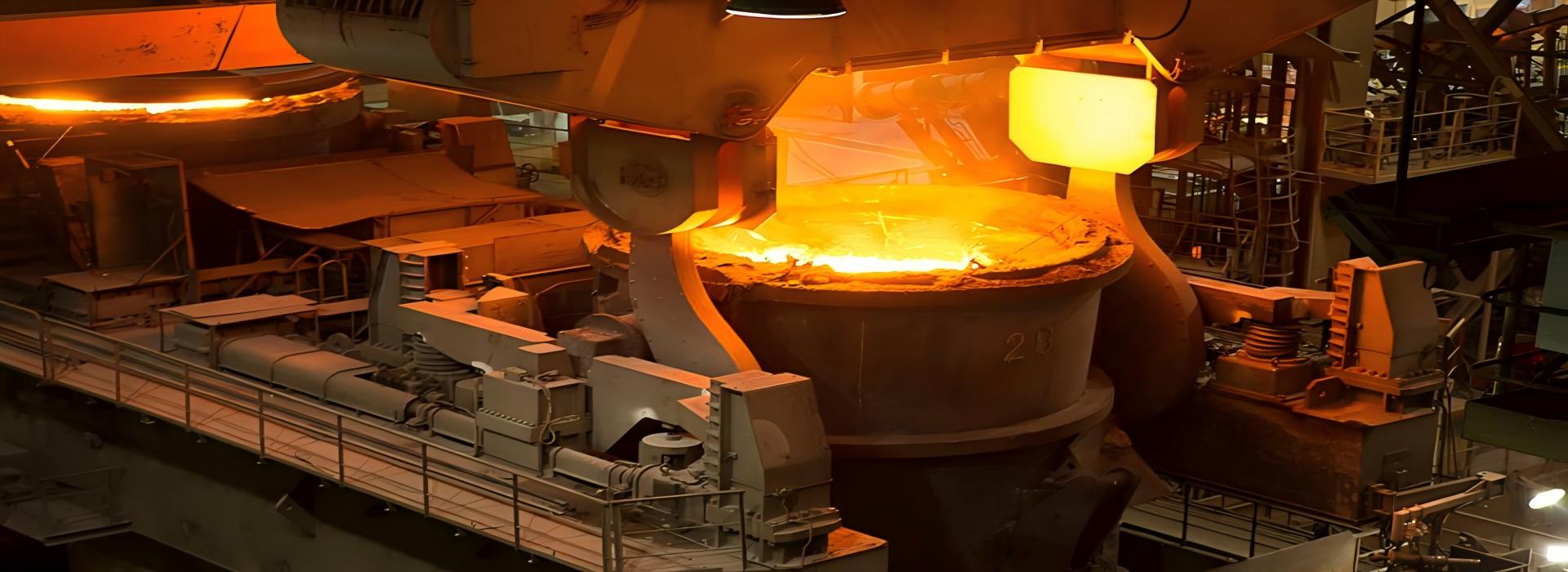
Shear Blade
Hydraulic shear blade for continuous casting is the core component of the hydraulic shear, and its performance directly determines the shear efficiency, kerf quality and equipment life.
- Commonly used materials
Hot work mold steel:
H13 (4Cr5MoSiV1): high-temperature strength, heat fatigue (800 ~ 1000 ℃), good wear resistance, suitable for high-load shear.
5CrNiMo: excellent toughness, impact resistance, suitable for frequent shear conditions.
Specialty alloys:
High speed steel (such as W6Mo5Cr4V2): high hardness (HRC 60~65), but brittle, need to optimize the heat treatment process.
Nickel-based alloys: high-temperature oxidation resistance (above 1100 ℃), used for shearing stainless steel and other high-alloy billets.
Surface coating technology:
Tungsten Carbide (WC) Coating: Enhance the edge wear resistance, life extension of 30%~50%.
Titanium Nitride (TiN) Coating: Reduce friction coefficient, reduce adhesive oxidized skin.
2.Performance index
High temperature hardness: maintain HRC 45~50 at 800~1100℃ (avoid softening and deformation).
Thermal fatigue resistance: withstand frequent hot and cold cycles (shear high-temperature billet → cooling) without cracks.
Wear resistance: reduce edge wear caused by friction with high temperature billets.
Toughness: to prevent chipping or fracture under shear impact load.
3., blade structure and design
Edge form
Flat edge: suitable for billet, slab, shear force distribution is uniform.
Beveled edge (5 ° ~ 15 ° inclination): reduce the peak shear force, suitable for large section billet.
Combined edge: the upper knife is beveled edge, the lower knife is flat edge, balancing efficiency and energy consumption.
4.Geometric parameters
Thickness of blade: 80~200mm (selected according to the demand of shear force, thick blade has strong deformation resistance).
Angle of cutting edge: 75°~90° (the smaller the angle, the smaller the shear force, but wear resistance is reduced).
Edge chamfer: 0.5~2mm (reduce stress concentration, prevent chipping).
5.Daily maintenance
Cooling lubrication: spray water-based coolant after shearing (avoid blade temperature over 300℃).
Cleaning of oxidized skin: regularly remove the iron oxide skin adhering to the blade surface (to prevent scratching the edge).
Wear monitoring: check the wear of the cutting edge every shift (more than 3mm need to be repaired and ground or replaced).
Edge resharpening: Use CNC grinding machine to repair the edge after wear to maintain the angle and straightness of the edge.
Our company has many years of experience in the production and marketing of Hydraulic shear blades, and we have professional technical personnel who can produce and process according to the individual needs of customers. The above parameter data can be used for reference, if you have specific needs, please feel free to contact us.