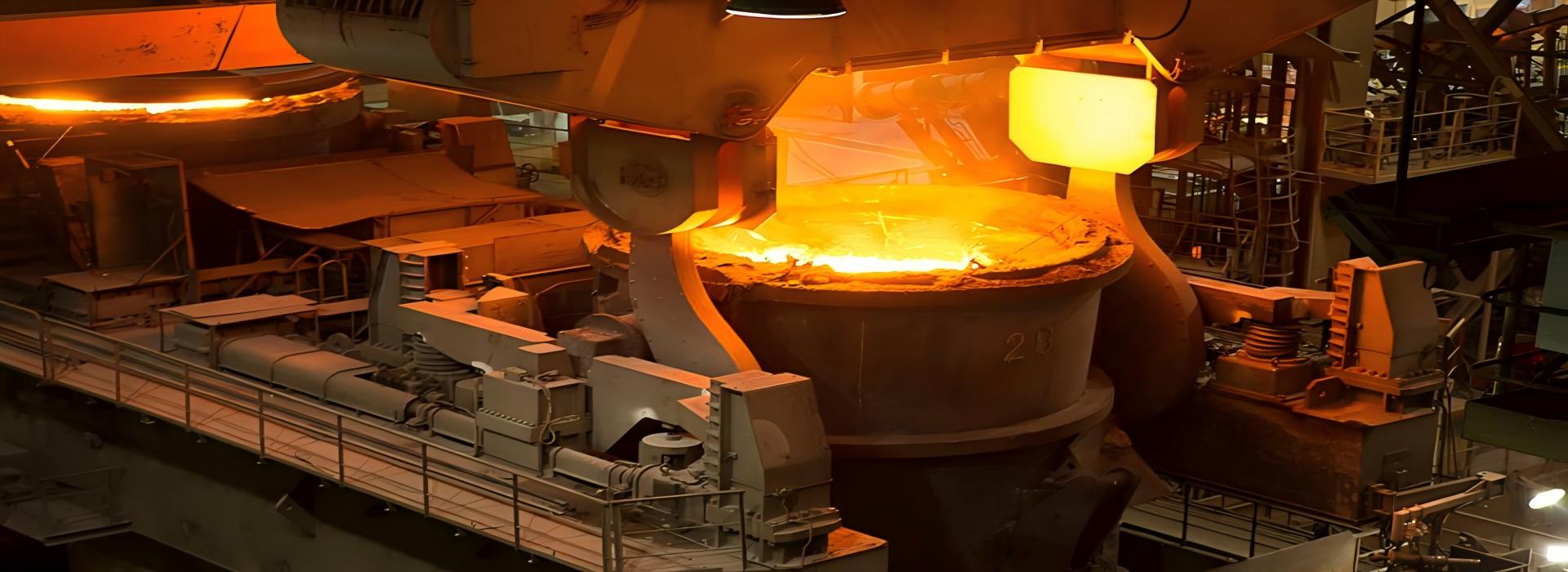
Secondary Cooling
The secondary cooling system of continuous casting machine (“Secondary Cooling”for short) is a crucial link in the continuous casting process, mainly responsible for further cooling and controlling the billet from the copper mold to ensure that the billet has an ideal temperature distribution and metallurgical quality in the solidification process.
1.Role of secondary cooling
Control of billet solidification: accelerate the solidification process of billet through cooling water or aerosol cooling to ensure that the billet is completely solidified when it leaves the continuous casting machine.
Regulate temperature distribution: through reasonable cooling intensity distribution, control the temperature gradient on the surface and inside of the billet, reduce thermal stress and cracks.
Improve billet quality: Reasonable secondary cooling process can reduce surface defects (e.g., cracks, depressions) and internal defects (e.g., shrinkage, segregation) in the billet.
Improve production efficiency: by optimizing the cooling intensity, the billet drawing speed can be increased, thus improving the production efficiency of continuous casting machine.
2.Key points in the design of the secondary cooling system
Nozzle arrangement: the arrangement of the nozzle needs to ensure that the cooling water uniformly covers the surface of the billet, avoiding the dead space of cooling.
Cooling uniformity: through the reasonable design of the nozzle type and spray angle, to ensure uniform temperature distribution on the surface of the billet.
Dynamic adjustment ability: the secondary cooling system should have the ability to adjust the cooling intensity in real time, in order to adapt to different steel grades, section size and billet drawing speed changes.
High-temperature and corrosion resistance: The nozzles and pipes of the secondary cooling system should be made of high-temperature and corrosion-resistant materials to prolong their service life.
3.Secondary Cooling System Maintenance
Regularly check the nozzles: clean the clogged nozzles to ensure the cooling water is sprayed evenly.
Check the water supply system: Ensure that the water pump, piping and valves are working properly to avoid affecting the cooling effect due to insufficient water supply.
Monitor the cooling effect: Evaluate the cooling effect of the secondary cooling system by using temperature sensors and the surface quality of the billet, and make adjustments if necessary.
Prevent water leakage: check the sealing of pipes and joints regularly to prevent cooling water leakage.
4.Secondary Cooling Process Parameters
Cooling water volume: determine the cooling water volume according to the steel type of billet, section size and billet drawing speed, usually expressed by the water volume per unit time (L/min) or specific water volume (L/kg).
Cooling mode: including water cooling, aerosol cooling and dry cooling (no cooling), aerosol cooling is currently the most widely used mode.
Cooling intensity distribution: the cooling intensity of different cooling sections should be optimized according to the solidification characteristics of the casting billet, usually the intensity of the upper cooling zone is higher, and the lower part is gradually reduced.
Surface temperature of billet: By controlling the cooling intensity, the surface temperature of billet should be kept within a reasonable range (usually 800℃~1100℃) to avoid cracks and deformation.
The main parameters | |
Spray form | Full water cooling, aerosol cooling |
Cooling zone | Set three to five independently controlled cooling sections according to process requirements |
Control way | Realize dynamic automatic water distribution according to drawing speed and temperature |
Our company has many years of experience in the production and marketing of secondary cooling, with professional technical personnel, according to the individual needs of customers, production and processing. The above parameter data can be used for reference, if you have specific needs, please feel free to contact us.