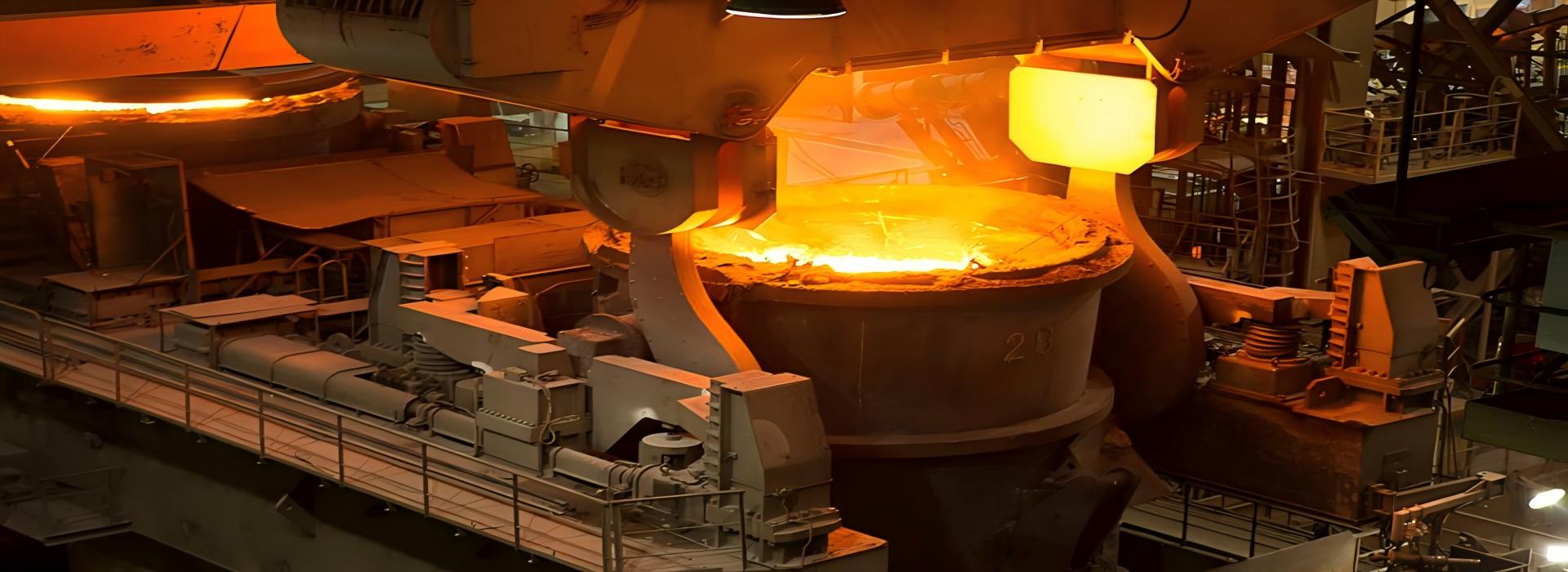
Roller Table
Roller table is one of the key components in continuous casting equipment, which is mainly used for supporting, guiding and conveying billets. It plays a vital role in the continuous casting process, directly affecting the quality of the cast billet and production efficiency.
1.Functions of Roller table
Supporting the billet: in the continuous casting process, liquid steel from the copper mold out of the gradual solidification, the roller table through a number of rollers to support the billet, to prevent its deformation due to gravity.
Guide billet movement: roller table through the roller rotation, guide billet along a predetermined path of movement, to ensure that the billet smoothly through the continuous casting machine sections.
Control of billet cooling: roller table usually with the cooling system, through the water spray or aerosol cooling billet, control its solidification rate and temperature distribution.
Prevent billet belly: in the casting billet has not been completely solidified, the roller table through a reasonable arrangement of roller spacing and pressure, to prevent the casting billet due to the internal static pressure of steel and the occurrence of belly deformation.
2.Roller table structure
Roller: The roller is the core component of the roller table, usually made of high temperature and wear-resistant materials. The arrangement of the roller has two types: segmented type and integral type.
Bearing and sealing device: It is used to support the roller and ensure its smooth operation, and prevent cooling water and iron oxide from entering the inside of the bearing.
Frame: The frame of the roller table is used to hold the rollers in place and is usually made of high strength steel to withstand high temperatures and mechanical loads.
Cooling system: Includes a water spray or aerosol cooling device to control the cooling rate of the billet.
Driving device: Some roll tables are equipped with a driving device, which is used to actively drive the rolls to rotate and help the billet to move.
3.Roller table design points
Roller spacing: According to the thickness of the billet and solidification characteristics of the design of a reasonable roller spacing, to prevent the billet belly and deformation.
Roller diameter: the diameter of the roller to meet the requirements of strength and rigidity, while considering the impact on the surface of the billet.
Cooling strength: the design of the cooling system needs to ensure uniform cooling of the billet to avoid cracks or internal defects.
Material selection: The roll and frame materials should be resistant to high temperature, wear and thermal fatigue.
Alignment accuracy: the alignment accuracy of the roll table directly affects the quality of the casting billet, need to ensure that the roll and casting billet center line alignment.
4.Maintenance of roll table
Regularly check the roller wear: rollers work under high temperature and heavy load conditions for a long time, easy to wear, need to be regularly checked and replaced.
Clean up the iron oxide: the roll surface is easy to accumulate iron oxide, need to be cleaned up regularly to prevent affecting the surface quality of billet casting.
Lubricate the bearings: Lubricate the bearings regularly to ensure the smooth running of the rolls.
Check the cooling system: Make sure the cooling water nozzles are smooth to avoid uneven cooling that may cause billet quality problems.
5.Common problems and solutions
Casting billet belly: may be the roller spacing is too large or the cooling intensity is insufficient, need to adjust the roller spacing or strengthen the cooling.
Cracks on the surface of the billet: it may be that the rollers are poorly centered or uneven cooling, need to check the precision of the roll table centering and cooling system.
Roller wear too fast: may be improper choice of material or cooling is insufficient, need to replace the higher performance of the material or optimize the cooling.
Continuous casting machine roll table design, manufacturing and maintenance of continuous casting production is critical, reasonable optimization of roll table structure and working parameters can effectively improve the quality of cast billets and production efficiency.
6.Parameter
Parameter | Slab Casting Machine | Billet Casting Machine | Shaped Billet Continuous Casting Machine |
Roller Diameter | 300~500 mm | 150~300 mm | 200~400 mm |
Roll Body Length | 1200~2500 mm | 800~1500 mm | Custom-made asymmetric structures |
Cooling Water Flow | 100~200 m³/h | 50~100 m³/h | 80~150 m³/h |
Driving Power | 30~100 kW/group | 15~50 kW/group | 20~80 kW/group |
Our company has many years of experience in the production and marketing of roller tables, with professional technical personnel, according to the individual needs of customers, production and processing. The above parameter data can be used for reference, if you have specific needs, please feel free to contact us.