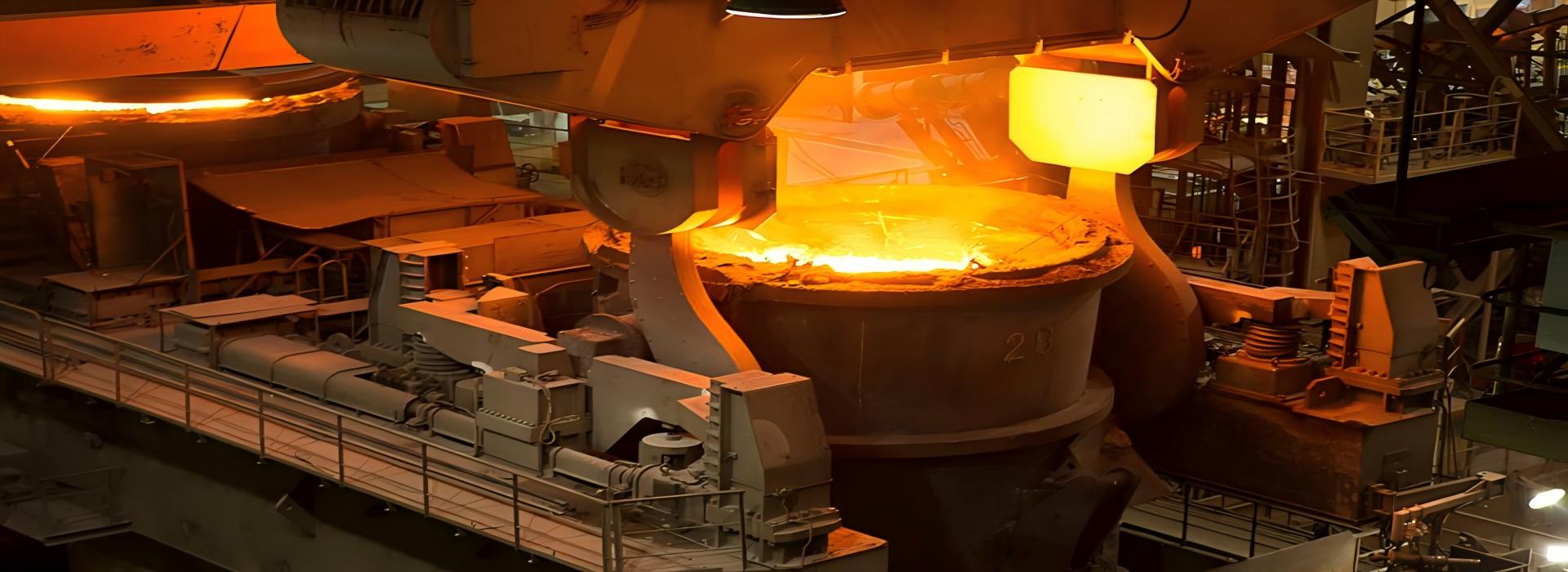
Hydraulic Shear
Hydraulic shear for continuous casting is a key equipment in the continuous casting (continuous casting) production line in the iron and steel industry, which is mainly used to cut the high-temperature continuous casting billets (e.g., billets, slabs, etc.) according to the set length with high efficiency and precision.
Structure and composition
1.Hydraulic system
Power source: high-pressure hydraulic pump station (including motor, oil pump, oil tank, etc.).
Implementing agency: hydraulic cylinder, through the hydraulic oil pressure to drive the shear blade to complete the shear action.
Control components: proportional valves, servo valves, etc., for precise control of shear force and speed.
- Shear mechanism
Upper and lower knife frame: made of high-strength alloy steel, high temperature and wear resistance.
Blade: special material (such as hot work mold steel), can withstand high temperature billet shear.
Guiding device: Ensure the precise movement trajectory of the blade to avoid offset.
3.Control system
PLC or industrial computer: realize automatic operation, set the cutting length according to the billet speed and process requirements.
Sensor: detect the billet position, temperature, shear force and other parameters, feedback to the control system.
Working Principle
1.Positioning of billet
Continuous casting billet is drawn to the hydraulic shear position by drawing machine, and the cutting point is determined by photoelectric sensor or encoder.
2.Cutting process
Hydraulic system drives the upper knife frame rapid downward pressure, and fixed lower knife frame to complete the shear.
Shear force can reach hundreds to thousands of tons, instantly cut off the high temperature billet (temperature of about 800 ~ 1100 ℃).
After shearing, the knife frame is reset, and the billet continues to be transported to the next process.
- Synchronized control
Synchronized with the continuous casting machine pulling speed, to ensure that the casting billet is stationary or low-speed movement during shearing, to ensure that the cut is smooth.
Core advantages
1.High efficiency
Shear cycle is short (usually 3-10 seconds), adapted to high-speed continuous casting production line (such as pulling speed of several meters per minute).
Compared with flame cutting, no gas consumption, energy saving and environmental protection.
- High quality of cut
Flat and burr-free cuts, reducing the amount of subsequent processing.
No oxidized skin generation, avoiding material loss.
- Automation and safety
Fully automatic control, reducing manual intervention.
Enclosed design prevents high temperature debris from splashing and ensures operation safety.
Application Scenario
Iron and steel continuous casting production line: for carbon steel, alloy steel, stainless steel and other cast billets cut to size.
Special working conditions: stable operation under high temperature and high load environment, adapting to different sections (square billet, rectangular billet, round billet, etc.).
Alternative to traditional processes: gradually replace the flame cutting and mechanical flying shear, especially suitable for high-precision, high-productivity needs of the production line.
Maintenance and common problems
1.Maintenance points
Regular replacement of hydraulic oil and filter element to prevent system contamination.
Check the blade wear, timely repair or replacement.
Lubricate the guide device to ensure the flexibility of moving parts.
2.Common Problems
Insufficient shear force: may be due to hydraulic system leakage or pump station pressure abnormality.
Tilted cut: caused by misalignment of the blade or wear of the guide mechanism.
Control system failure: need to check the sensor signal or PLC program logic.
Reference parameters
- Shear force range: 500 tons ~ 5000 tons
(adjusted according to billet material, section size and temperature).
- Section shape: square billet, rectangular billet, round billet, slab, etc;
- Section size:
Billet/rectangular billet: 100×100mm~600×600mm;
Slabs: thickness 150~400mm, width 1000~2500mm;
- Temperature range: 800 ℃ ~ 1100 ℃
(high-temperature shear requires special material blade).
- Shearing cycle
Single shear time: 3 ~ 10 seconds (including blade closure, shear, reset);
Continuous shear frequency: 6 ~ 20 times / min (and continuous casting machine speed match).
- Shear precision
Length error: ± 2mm ~ ± 5mm (affected by synchronization control precision);
Cutting flatness: ≤1mm/m (no burr, no crack).
Our company has many years of experience in the production and marketing of hydraulic shears, with professional technical personnel, according to the individual needs of customers, production and processing. The above parameter data can be used for reference, if you have specific needs, please feel free to contact us.