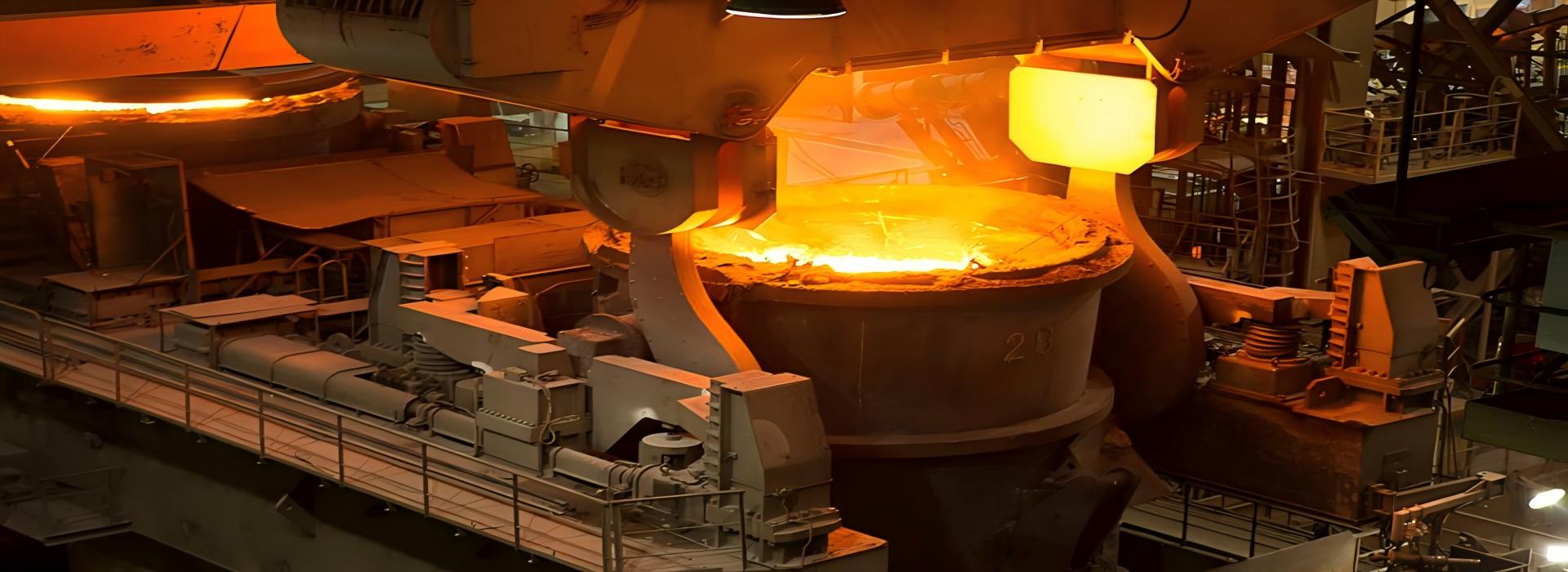
Dumny Bar Storage
Dummy bar storage is an important link in continuous casting production, which directly affects the equipment life, production efficiency and safety. Reasonable storage design and management can reduce the risk of deformation, corrosion and collision, and ensure the fast call and stable operation of dummy bar.
1.Type
type | design feature  | superiority |
Fixed storage frame | Steel structure platform + positioning card slot, Dummy Bar horizontal placement | Simple structure, low cost, suitable for small continuous casting machine |
Mobile car | With walking wheel and hydraulic lifting mechanism, can switch | Flexible adaptation of multi-flow continuous casting machine, save space |
Folding suspension frame  | Dummy Bar Vertical suspension, folding through the hinge for storage | Reduce the footprint, suitable for the compact workshop layout
|
2.Storage operation specification
Cooling requirements: dummy bar After use, it should be cooled below 80℃ before storage to avoid deformation caused by thermal stress.
Ambient temperature: storage temperature 50℃ (away from high temperature sources such as molten steel bag and refining furnace).
Positioning accuracy: store the rack positioning error of ± 2mm to prevent dummy bar bending or collision damage.
Surface protection: spray anti-rust oil (such as lithium grease) and cover to avoid oxidation corrosion.
Isolation measures: the storage area is fenced with a distance of 1.5m.
Anti-collision design: add rubber cushion (30mm thickness), impact resistance energy 500J.
3.Maintenance and testing specification
project | period | method | standard |
Geometric size detection | Once a month | The laser scanner measures the straightness and curvature | The straightness is 1mm / m, and the total bending length is 0.1% |
Surface injury examination | Once a week | Visual + magnetic particle detection (focus on head and connection) | The crack length is 5mm, and the pit depth is 2mm |
Cooling system detection | Once a quarter | Pressure test (1.5 x working pressure for 30 minutes) | Pressure drop of 5%, with no leakage |
Anti-corrosion layer evaluation | Once every six months | Coating thickness gauge (random 10-point measurement) | Thickness 0.1mm, peeling area 3% |
Functional test | Once a year | Simulated storage-call cycle (10 times) | Positioning accuracy, locking force attenuation of 5% |
4.Common problems and resolution strategies
fault phenomenon | primary cause | Rx | preventive measure |
Dummy Bar Deformation | Insufficient cooling or uneven support | Thermal straightening (800-900℃ pressurized repair) | Optimize the cooling water distribution and increase the intermediate support points |
Surface rust | Failure of antirust coating or too high environmental humidity | Anti-rust paint after sandblasting | Dehumidifier is installed in the storage area (40% humidity) |
Positioning offset | Settlement or loose vibration of the storage rack foundation | Replace the foundation (strength C30) and install the damping pad | Monthly check of anchor bolt torque (design value 90%) |
The card block cannot be removed | Thermal expansion causes the stuck slot deformation | Local air cut expansion tank + wear-resistant lining plate repair | Reserved expansion clearance for card slot (0.5~1mm / m) |
Our company has many years of experience in the production and marketing of dummy bar storage, with professional technical personnel, according to the individual needs of customers, production and processing. The above parameter data can be used for reference, if you have specific needs, please feel free to contact us.