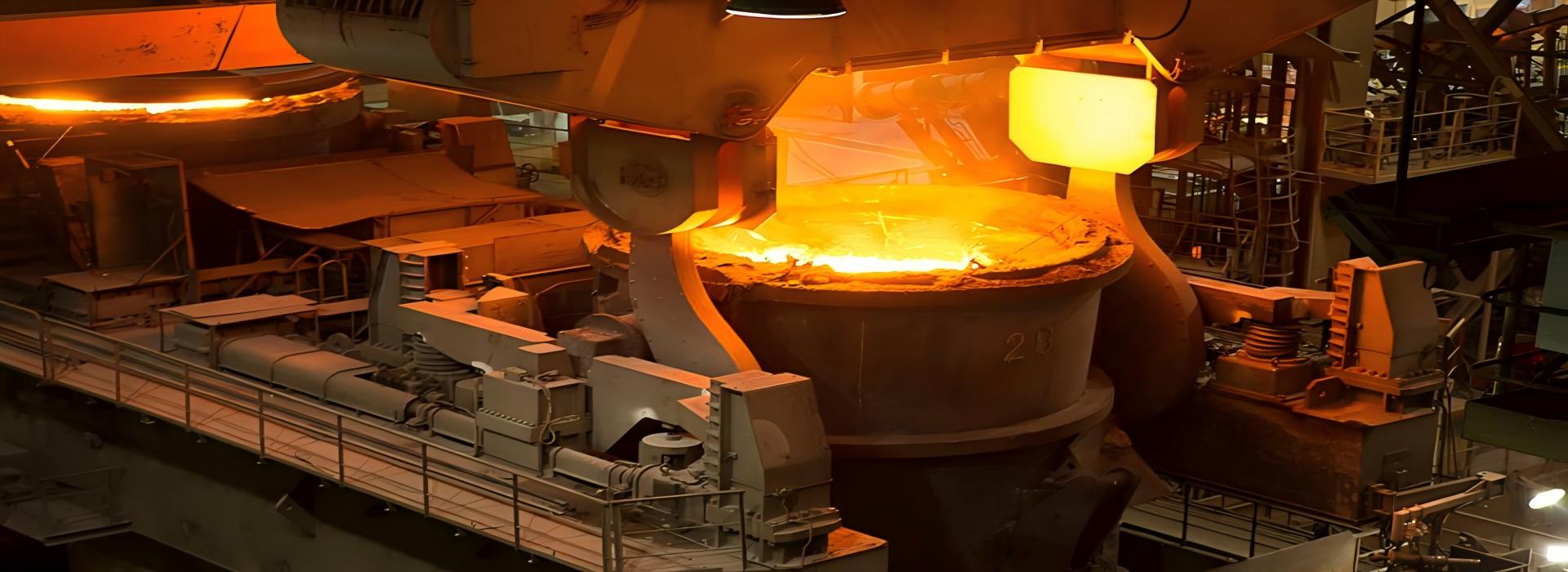
Dummy Bar
The dummy bar is the core equipment in the start-up phase of the continuous casting machine, which is responsible for guiding the transition of the billet from copper mold to the withdrawal straightening machine, and safely detaching the billet after solidification. Its design and storage directly affect the stability and efficiency of continuous casting production.
Core function
- Initial guidance: when the continuous casting starts, the dummy bar head is sealed with the copper mold to form the initial billet shell, which pulls the billet into the drawing machine.
2.Transmission of tension: withstand the tension of the withdrawal straightening machine (usually 20~100 tons), to ensure that the billet is continuously and stably pulled out.
- Safe detachment: when the billet solidifies to a sufficient strength, the dummy bar and the billet are automatically separated to avoid equipment damage.
Types
- Rigid dummy bar: Integral casting or welded steel structure, high strength, no moving parts, suitable for billet, rectangular billet and other simple surface continuous casting machine.
- Semi-rigid dummy bar: segmented articulated design, allowing local bending, suitable for slab continuous casting machine (need to adapt to the change of width-thickness ratio)
- Flexible dummy bar: chain type or plate spring type structure, applicable to arc / oval continuous casting machine (such as small radius arc machine)
Structure and key components of dummy bar
- Rod material: high-temperature-resistant alloy steel (e.g. 42CrMo), with heat-resistant coating (e.g. Al₂O₃) sprayed on the surface.
- Rod section: rectangular (for slab) or round (for billet), width/diameter 200~600mm.
- Dovetail groove locking mechanism: to realize quick sealing with copper mold (sealing pressure ≥5MPa).
- Graphite inlay block: reduce the adhesion with billet, easy to detach.
- Guide roller group: arranged on both sides of ingot-inducing rod, adopting water-cooled rollers (roller surface temperature ≤150℃) to ensure precise movement trajectory.
- Cooling system: internal water cooling pipe (water pressure 0.6~1.2MPa) to prevent high temperature deformation.
- Disengagement mechanism: hydraulic push device (thrust 50~200kN) or mechanical jaws, to realize the rapid separation of billet and dummy bar.
Regular maintenance
- Geometric dimension inspection: Measure the straightness of ingot-inducing rod every month (deviation ≤1mm/m) and the wear of head (≤3mm).
- Seal check: quarterly test the pressure of cooling pipe (pressure drop ≤5% for 30 minutes).
- Function test: simulate detachment action (2 times a year), verify hydraulic/mechanical system response time (≤2 seconds).
Common problems and countermeasures
- Dummy bar alignment deviation: guide roller wear or copper mold installation offset, replace the guide roller bushings, laser calibration of the copper moldposition.
- Failure to disengage: insufficient hydraulic pressure or jammed claw mechanism, check the hydraulic station relief valve, clean the claw guide rail
- Head sticking to the billet: graphite block loss or insufficient cooling, replace the graphite inlay block, optimize the cooling water flow.
- Bending and deformation of the rod body: thermal stress concentration or unreasonable storage support, increase the intermediate support point, and repair by hot straightening.
Selection and use of recommendations
- Matching continuous casting machine type: billet continuous casting machine preferred semi-rigid dummy bar, billet continuous casting machine selected rigid dummy bar.
- Balance between capacity and maintenance: high operating rate production line (>85%) is recommended to use mobile storage device to improve the turnover efficiency.
- Low and medium capacity workshop can choose fixed storage rack + regular outsourcing maintenance, reduce the initial investment.
Our company has many years of experience in the production and marketing of dummy bar, with professional and technical personnel, according to the individual needs of customers, production and processing. The above parameter data can be used for reference, if you have specific needs, please feel free to contact us.