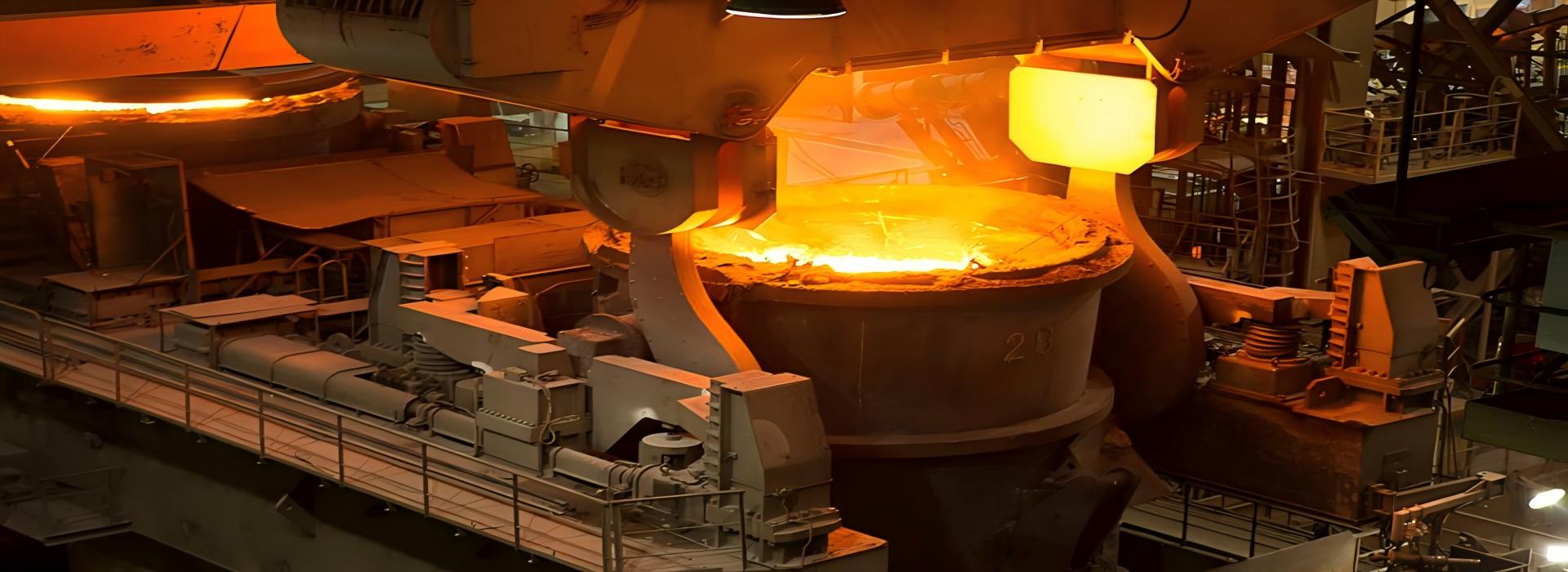
Copper Mould Assembly
Continuous casting machine is the key equipment in steel production, and copper mould assembly is the core component of continuous casting machine. Its main role is in the continuous casting process will be liquid metal gradually cooling solidification, the formation of continuous billet. Through the cooling system of copper mould assembly and the control of liquid metal, it can meet the production needs of different process requirements and billet specifications, and at the same time, it can also improve the quality and performance of products.
- Functions and roles
Initial solidification: After the steel flows from the tundish into the copper mould, it is cooled rapidly to form a uniform billet shell of a certain thickness (usually 10-30 mm), which ensures smooth billet drawing in the subsequent secondary cooling section.
Heat transfer and lubrication: The heat is rapidly exported through the copper wall and cooling water, and the slag is protected to form a liquid lubrication film on the surface of the molten steel, which reduces the friction between the billet shell and the inner wall of the copper mould.
- Structure and type
Material selection:
Inner wall: high purity copper or copper alloy (such as Cu-Cr-Zr), plating (chromium, nickel-cobalt alloy) to improve wear resistance and oxidation resistance.
Shell: stainless steel or high-strength steel, internally designed cooling water channels.
Common types:
Tubular Copper Mould: Integral copper tube structure, suitable for small section billet casting (billet, round billet).
Combined Copper Mould: Multiple copper plates assembled, adjustable taper, for slabs or shaped billets.
3 Common problems and solutions
Steel leakage: uneven thickness of billet shell, poor performance of protective slag, alignment deviation.
Measures: Optimize the viscosity of protective slag, adjust the vibration mode (e.g. non-sinusoidal vibration), strengthen the liquid level control of the crystallizer.
Plating wear:scratches on the inner wall, decreased thermal conductivity.
Maintenance: Regular inspection of plating thickness (usually ≥0.1mm), re-plating or replacement of copper plate after wear exceeds the standard.
Thermal deformation of countermeasures: Optimize cooling water distribution, use high thermal strength copper alloy materials.
- Maintenance points
Daily inspection:
Cooling water hardness (avoid scaling), pressure (0.6-1.2MPa), temperature difference between inlet and outlet water (≤8℃).
Copper plate surface roughness (Ra≤0.8μm) and taper accuracy (error <0.1mm/m).
Lifetime management:
Record the amount of steel flux, combined with the depth of thermal fatigue cracks (more than 2mm need to be replaced).
The design and operation of copper mould directly affects the operating rate of continuous casting machine and the quality of cast billet. In modern continuous casting process, its optimization direction focuses on high efficiency heat transfer, longevity and intelligent monitoring, in order to reduce production cost and adapt to the demand of high drawing speed (e.g. slab drawing speed up to 2.5m/min and above).
- Key design parameters
Taper design:
The inner cavity gradually shrinks along the drawing direction to compensate for the shrinkage of the blank shell (e.g., the taper of the slab is usually 0.8-1.5%/m).
Cooling strength:
Water slit width: 4-6mm, water flow rate 6-12m/s to ensure high heat flow density (up to 2-3 MW/m²).
Vibration parameters:
Hydraulic or mechanical vibration, amplitude 3-10mm, frequency 50-200 times/minute, preventing billet shell sticking.
Arc radius | R4000~R14000mm | |
Casting size | Billet | 100×100~350×420mm |
Round billet | Ø120~Ø800 | |
Slab | 140X300~750 | |
mould type | Billet/round billet | Tubular |
slab | Plate type | |
taper | Single taper, multiple taper or parabolic taper | |
Inner water jacket form | Integral stainless steel tube type, finishing assembly type |
Our company has many years of experience in the production and marketing of copper mould assemblies , with professional technical personnel, according to the individual needs of customers, production and processing. The above parameter data can be used for reference, if you have specific needs, please feel free to contact us.